UPDATE ON LABORATORY OPERATIONS
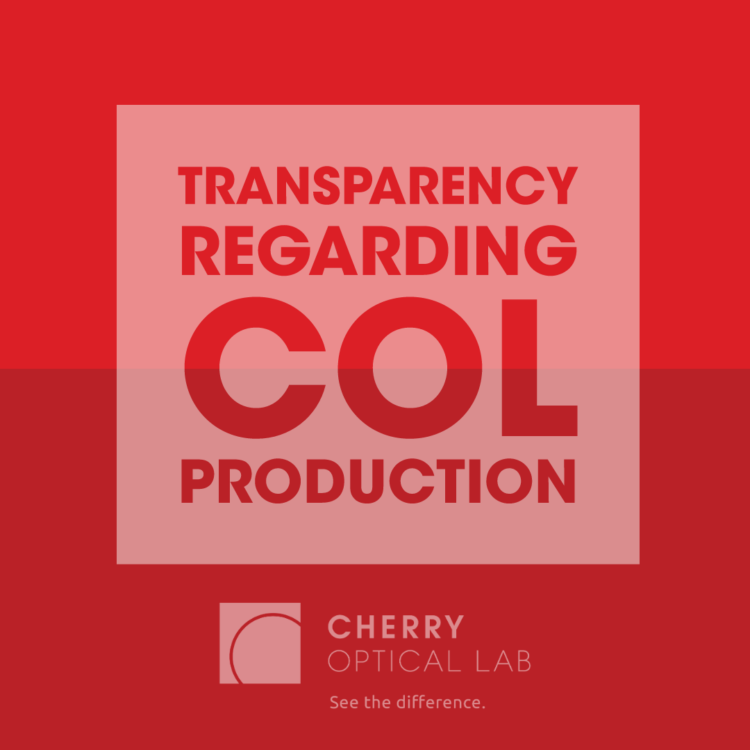
August 9, 2020
UPDATE ON LABORATORY OPERATIONS
It seems surreal, but it has already been a month since our last communication about the status of production at Cherry Optical Lab. We have a significant update to share that is mostly positive. As promised, we will not hide, and we will provide full transparency to ensure we all have the same expectations.
Thankfully, while infection numbers continue to climb, we have not seen mass hospitalizations and deaths that would cause a state or region to be shutdown. We are also extremely thankful that none of our extraordinary employees have contracted Covid-19.
We continue to see more citizens getting in line with utilizing the necessary PPE to mitigate the spread of infection. We believe these essential precautions are vital to allow incoming new order volumes to remain strong. We are grateful for our situation and appreciate all our outstanding customers across the country. Above all, we want everyone to stay safe, healthy, and open!
We are pleased to share some very positive news. Our Satisloh 1200-DLX-2 vacuum box coater (1200) is installed and has been producing anti-reflective lenses since 7/31. The impact of this new AR coating chamber is colossal and has us confidently headed towards a return to normal service levels in the coming weeks. Our Coating Team did a tremendous job over the past ten days to maximize the utilization of the new 1200, and the two existing chambers, beyond my highest expectations. Our coating operations had a massive backlog building, peaking on 7/30, but with unbelievable dedication, the Coating Team has its work-in-process at optimal levels. The amount of work completed in the past ten days was critical to getting back on track.
The most immediately impacted orders with the addition of the 1200 are uncuts. Service levels on uncut orders have returned to normal and are averaging under 2.3 days. We expect our uncut service levels to maintain these levels with slight improvements from day-to-day.
Edged orders have also benefited; however, the glut of work that was at coating has now found its way to first-inspection, edging, assembly, and final inspection stations.
A backlog “at finish” is positive, in my view, as it means the work is backed-up at the finish line, not at lens inventory and coating as it was through much of July. The average turn time on edged work climbed week-over-week, peaking the week of 7/27. Out of 8,525 edge jobs shipped or in-process starting 8/3, the average time for frames to arrive was 2.1 days, and the average days in-process was 3.7 days for a total average turn time of 5.8 days. Full disclosure, I do not expect this number to improve considerably. It is likely to see an increase before leveling off and ultimately getting back to normal around the end of August.
All-in, average service levels for jobs shipped and in-process is 4.8 days.
We still see more backorders from our lens suppliers than usual, and we have received notifications from nearly all the major lens manufacturers to expect disruptions through August. I would anticipate their distribution issues to continue into September. Our backorder woes peaked the week of 7/20. Our Customer Service and Inventory Teams made constructive adjustments to our handling of backorders. We feel confident that we can find viable alternatives and recommendations to our customers to avoid unnecessary delays.
You do not have to search too hard to find stories about the stress on logistics, trucking, and inventory for nearly all industries. We encourage you to set customer expectations at 8-12 days to avoid disappointment and remind patients that “the world” is trying to get rolling again. Manufacturing during a pandemic is not optimal. Stopping production and then restarting it at blistering rates of demand, within three months, is not going to be as fruitful as we would all like it to be. Everyone recognizes that even something as basic as Clorox wipes have not been consistently available for months. Consider asking patients to extend a bit of patience. Let them know we will provide them with exactly what they want, albeit in a slightly longer timeline than usual.
Cherry Optical Lab is well organized, and we are doing everything humanly possible to complete as many orders as we can each day. We are sticking to a stringent first-in, first-out prioritization system. We understand that some orders need to be expedited, and we will do our best to meet your requests. Please only request a ship-by date if it is vital. We are keeping an eye on rush orders to ensure it is not being abused. Overuse of rush ordering only makes meeting vital requests more difficult. I believe there is a story about a boy and a wolf that should clear up what we are saying here.
This past week we began holding wait-for-frame jobs from immediately being put into production to ensure our processing energies are utilized to give uncut and orders with frames on-site our full attention. This temporary change has shown positive results to the point that we are releasing some wait-for-frame orders late at night into the early mornings to keep digital surfacing and coating operations rolling 24 hours per day.
We have added more than a few new employees and have more coming on board weekly. The continued additions will fill in all department needs for all shifts. The contributions of our new hires are starting to show. When onboarding and training a new hire, there is a lag in output as our top people must teach. Our experienced employees are doing an excellent job of sharing the training responsibilities to help balance production needs while also making our new people comfortable and confident. Quality remains most imperative to us, and we are pleased to say that we are still achieving our goal, in which 99+% of jobs that are shipped are not returned due to laboratory errors. We will not sacrifice quality in exchange for speed or quantity of orders shipped.
The last update we have for you is on our expansion project. The expansion continues to run smoothly, and it could not be coming to the next phase at a better time. The big wait right now is on the utility company to changeover and activate our new electrical service. When power is supplied, we will be hanging lights, finishing floors, and preparing to open walls to connect the current building to the expanded space. The tentative schedule for occupying the new space is the end of this month. When we can legally occupy the addition, there will be much work to do, but thankfully a lot of that work will be adding new equipment and workstations that will only make us faster.
To wrap this up, I want to first-and-foremost thank the amazing employees here at Cherry Optical Lab. Their drive and dedication are truly remarkable. All of us at Cherry then want to thank you, our supportive customers, and business partners. We appreciate your understanding and confidence in us. As we prepare to enter our sixth month of Covid-19, it finally feels like the light at the end of this mess is getting closer. By making smart decisions, being flexible and understanding, and working our asses off, we will come out the other side of this better, more powerful, and well prepared to continue as the best optical laboratory.
Please contact me at adamcherry@cherryopticallab.com, O: 920-469-2559 or C: 920-217-0249 if you would like to discuss the state of operations at Cherry Optical Lab or the eye care industry in general; there sure is a lot going on right now!
-Adam Cherry
Download the PDF: Update on Operations August 9, 2020
Categories